Engineered Quartz (ES)
By Mark Ortiz, Stone Restoration Specialist
This months subject is awareness of the common issues of engineered quartz, also called engineered stone (ES), right after installation. Realizing I'm speaking to a wide audience I'll keep my explanations easily understandable to the newly acquainted. I've been giving my perspective and sharing my experience of Engineered Quartz here in Southern California for the last 10 years. It's important to note that I don't sell or install engineered quartz, or ever plan to, therefore if I seem to step on your toes a little and thought we were friends, well, we're still friends but I will always do my best to give the facts and carefully consider my opinions.
My personal quote is that, "One can make better decisions for themselves once they have the truth, even if the truth is not always pleasant to hear." So let's get on with some truths about engineered quartz!
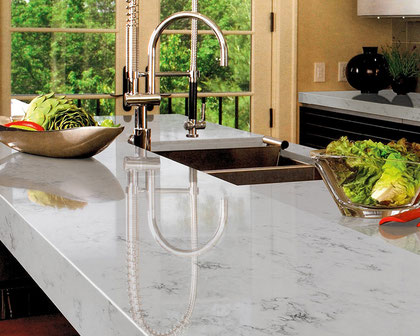
Here are some of the truths about man-made Engineered Quartz. It's a mixture of hardened resins/plastics and other additives such as natural stone, glass, metals and whatever else they can recycle.
Not all engineered surfaces are the same yet there are some similarities. Most don’t easily scratch, most don’t stain, most don’t etch from acidic liquids, and few can be restored. “What do you mean, few can be restored?”
I want to be real here 'friends'. ES is not bulletproof no matter what the creators of quartz or marketers may claim and now allude to. Problems happen to ES just like any other countertop surface. Due to its composition the repairs are difficult and surface polishing rarely matches the factory finish like other tried and true products such as marble and granite.
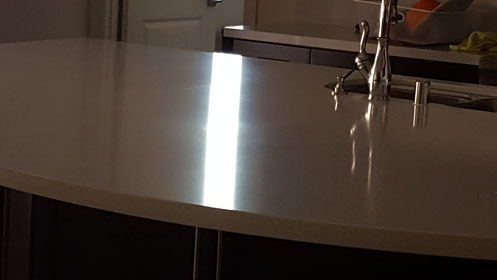
Inconsistencies in Reflection
ES is not blemish free. Customers should be aware that blemishes such as streaks, dullness, scuffs, pits and color contaminants are common on newer installations. ES is basically a mixture of 93% stone aggregates and 7% resin polymer (by weight, not volume). It is mixed together like a pan of rice crispies and buttered marshmallows. The mixture is pressed down and heated until all the air bubbles and voids are removed, cooled and refinished to a high polish. So if you are being intellectually honest, do you really expect it to be BLEMISH FREE? Let's look at some common issues for new installations.
If you look closely at the picture you will see dull blemishes in the reflection. Hard to see both in pics and in person.
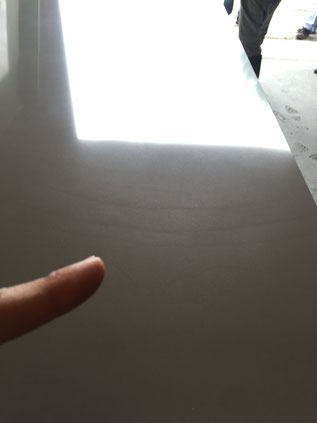
Lighting reveals the blemishes
After installation we often see blemishes on the surface via natural lighting. It's very difficult to see blemishes, this is why fabricators could not see it prior to installation. Lighting changes everything! Outdoor lighting that reflects off the countertop reveals inconsistencies more than any other lighting. Sometimes homeowners will turn off their artificial lighting to see the blemishes more clearly. This is why the counter looks 'as expected' before sunrise or after sunset. Because outdoor lighting is the primary factor, most of the complaints i get are in kitchens. The picture shows dull rib like shadows.
This is not an excuse but a fact... Inconsistencies in factory finishes are common and are to be expected!
Sometimes it's not factory blemishes, and this is where it gets, well, sticky and people start to point fingers.
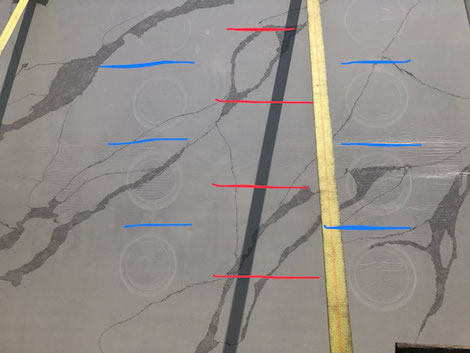
Large rings or circles
When we get a call about large rings on ES the first assumption from customers is that it's from 'suction cup rings' used at the factory. It's true that the factory and some fabricators use suction cups to lift slabs but that isn't always the case. To help see this, the photo to the right shows what factory circles look like on the back side of the slab. These are circles on the plastic protector yet similar markings on the front. They are evenly spaced, approximately 10 inches in diameter and throughout the slab. Red lines point to circles, blue lines are spaces in between. The best reason explained to me why this occurs is that the slabs may not have been completely cured prior to lifting because suction cups do not harm the surfaces. Sometimes the rings can be cleaned off but if it is more than skin deep, it may be permanent.
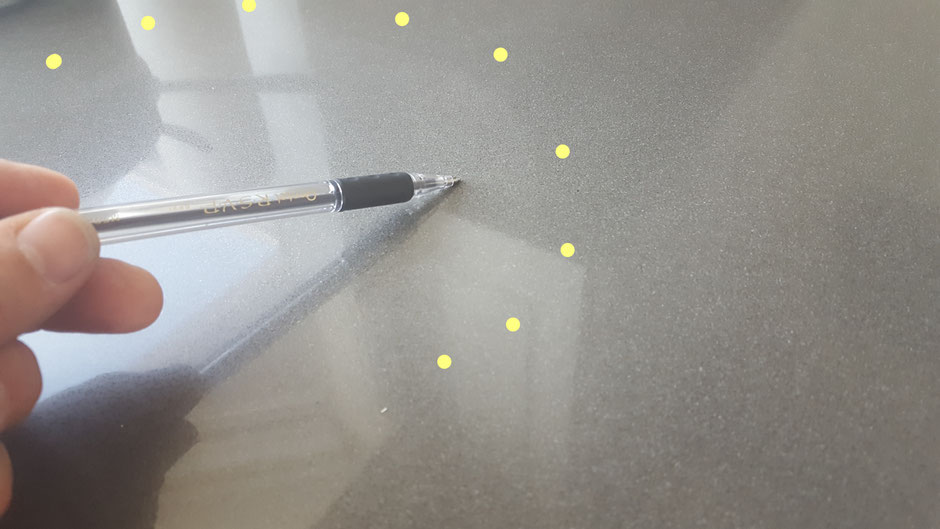
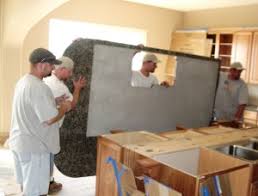
The poor fabricator.
Stop right here....and accept the conclusion, that until now, the blemishes had nothing to do with the fabricator.
Fabricators are the whipping boys of the stone industry. They handle the material more than anyone else. They drive it to the shop, unload and move them, lay them on a bridge saw table, re-lift and place on lamination tables, pick up again and place in their truck. Drive to the job, carry it in and sometimes walk up 3 flights of stairs, set it on cabinets, level as best as possible and fill joints. Sometimes a slab may require up to 6 strong men to move these around. These guys deserve an applause!
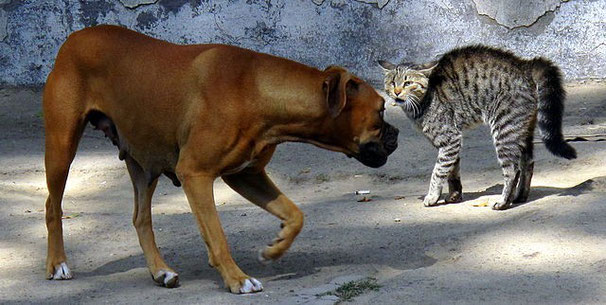
One piece of advice and consideration...do not initially put the blame on fabricators and installers for every issue on the surface of engineered quartz and natural stone.
Get the facts before unpleasantries come out out your mouth or a bloody showdown ensues. Stuff happens (chaos) and solutions follow (order).
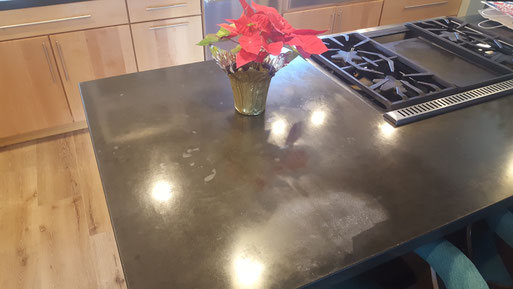
Installers can scratch the surface
Installers are not out of the woods in all cases because 'stuff happens'. The most common issue is scuffing the surface with their abrasive diamond pads to finish the edges off or remove a scratch. These diamond pads scuff and dull the surface pretty easy and if the material is wet, it's impossible to notice until it's dry or the light reveals it.
Some fabricators have the skill and patience to remove these blemishes but most don't because the products and techniques are not available to them and because it's so darn difficult and usually impossible to restore the factory polish on ES!
Sometimes the installer is convinced he can remove the scratch or other issues without realizing the problems that he'll discover. Yes, I did say "he" because a "she" would stop and say, "Hey, let's get PGS out here to fix this." (You know I'm right.)
The picture is an example of a surface sanded by the installer. PGS is able to restore the polish but we never claim we can make it match perfectly. This time I don't think the flowers lessened the blow.
FINAL THOUGHTS
“Engineered Stone is an excellent choice for counters yet it’s not bullet proof and needs to be cared for properly. It is common to see light blemishes immediately after installation depending on the lighting in your home or office. Try to keep high heat away from it. It hasn’t been around as long as natural stone therefore any repairs or polishing is difficult, according to the professionals.”
I didn't have time to go into all the issues or concerns regarding engineered stone, but over time I will. PGS has been repairing engineered quartz since its inception to the industry so call ☎ (714-999-2961) us if you have any questions or run into an issue.
Please let me know what you would like to see in our newsletters. Thank you for referring Perfect Granite Solutions, the stone and quartz restoration experts.
Pass this useful information to your staff and everyone associated with the stone industry. Let us know if you want to be added to our Monthly Education Newsletters by entering your email at the bottom of the home page.
Do you have a topic that the industry needs to know about? Email it to me: mark@perfectgranitesolutions.com
Susan (Tuesday, 12 August 2025 18:44)
Hi! Tiny dark blue, black dots are appearing on our quartz surfaces. Our shower walls, bathroom and kitchen counter tops are all Silestone Nolita Suede. They were installed several months ago. What are your thoughts on this issue? Thank you!
Mark Ortiz (Wednesday, 09 April 2025 13:58)
Christina- with the risk of someone getting a spanking… you might have an engineered stone that is more dominant in marble verses quartz. If that’s true (and I don’t know for sure yet) then you need to go back to the supplier and determine if that was stated. Do the lemon test. Set a lemon wedge on the counter for about 5 min. If it dulls the surface then I’m probably right. You need to bring the contractor and the supplier to show them at the same time what’s going on. If it doesn’t dull the surface then have you tried scraping the spots off with a flat razor blade? Email me at mark@ortizstonerepair.com so we can try to resolve this sooner. Thanks!
Cristina (Monday, 07 April 2025 18:53)
About 6 months ago we had engineered stone counters installed per our contractors recommendation. It’s been a nightmare as our hard tap water causes etching immediately, which has been impossible to avoid, so our new counters are full of rings, splotches and other unsightly marks that aren’t visible in daylight but are pretty obvious in artificial light. The marks feel rough to the touch and nothing works to get rid of it, I assume the tap water reacted with the stone and damaged the finish somehow. Is there any hope for professional restoration and an extra sealant we can apply to stop this nightmare or are we doomed to eventually replace with with something more expensive?
Mark Ortiz (Sunday, 23 March 2025 07:28)
Robert and Megan - I'm so sorry I missed your requests. Yes, email me at : mark@ortizstonerepair.com and I can help you further, if you haven't already took care of that.
Robert, clear like bubbles could be a few things, but I would first scrape off with a straight edge razor blade, then clean with denatured alcohol. That should do it. Let me know if it did not..
Megan - If the quartz is pitted, then you will need to have it filled. I might be able to help you with that.
email me!
Megan (Monday, 10 March 2025 23:46)
Hi! A lot of good info in your comments, thanks for replying to so many!
I have quartz in my kitchen and have 2 issues. One is my own fault, I think… I was doing a craft with super glue - with paper and paper towels between the countertop and my items being glued, but I noticed now what looks like maybe chemical damage to the top of the counter? The shapes are similar to what I was gluing so that’s why I think it’s from that, but as I said, I did have paper down. Do you think the super glue fumes or off gassing caused damage? Is there a way to repair it? Very frustrated at myself.
Secondly, we’ve had these countertops going on 3 years and just recently at one end there are some weird circles that are under the top layer, don’t wipe off, and came out of nowhere. Is that even possible or is it some sort of damage? Although I’m real careful about hot pots and plates and anything that could scratch them… I’d love to send you a couple photos for your advice.
Thanks so much for your time.
Robert Latt (Tuesday, 21 January 2025 14:36)
Hi , I live in Northern California. My new ( 4 days) White Slabs for the kitchen countertop and back splash have some type of what appears to be sprayed micro bubbles. It is almost as if some one used a spray can and left a light consistent spray of translucent bubbles on the surface. I have cleaned it with water, soft micro fiber etc.
I am preparing for the "its the mfg" or its the " fabricator" or its the " installer when I reach out to my GC. Do you know what this phenomena can be? Thank you so much!
Mark Ortiz (Thursday, 16 January 2025 09:56)
Hello Pat. Mendoza Marble or Perfect Granite Solutions can polish up the quartz for you. Once you polish quartz you cannot bring it back to the original factory reflection. A high polished finish will look more like marble.
Carol. Thats a lot of spots... I would lay the sample they gave you on top and compare, as I'm sure you did. There is no exact quantity of spots per area I can give you, that would qualify as too much, but maybe there is something in the contracts about it. If there are over 20 spots on the entire slab, I would request some replacement, but a simpler answer is to have those spots dremeled out and refilled with an epoxy / resin. It works really good. I'm guessing the cost will be between $1000-$1500 depending on quantity and location.
Carol R (Tuesday, 14 January 2025 13:05)
Hi Mark. Is there an industry standard for how many of the small black dots created during manufacturing are acceptable for quartz countertops? My bathroom countertop is roughly 13 sq ft and it has over 35 of these dots on it. My kitchen has so many of them - I can't count them all (3-4 per sq foot like the bathroom). When I talked to my GC and the countertop guy they said the dots are part of the manufacturing process and there is nothing they can do. But, it just seems like there should be a standard on how many can appear per sq ft - mine seem excessive.
Any advice you can offer would be greatly appreciated.
Pat Ventura (Saturday, 04 January 2025 15:15)
Please recommend a company that has polish my quartz countertop to a high polish finish. I live in Palm Springs. Thank you
Mark Ortiz (Tuesday, 31 December 2024 23:15)
Hi Roxanna. I'm not sure what a resin powder is. If there was a name for the product, it might make more sense to what it is. There are some cleaning products with powder, but again, I'm not sure what it is. I would stick with Barkeepers gel cleaner if your blemishes are light, it will not damage the surface. Always use a non scratch scrub sponge. As far as those dull spots when the natural light comes in...if it is not to bothersome, then I would leave it alone. There is no damage to the surface, it just can be annoying to some people for the time the sun reflection hits it. If you want to get more information, email me at mark@ortizstonerepair.com. Thanks.
Roxanna (Tuesday, 31 December 2024 08:38)
Mark,
We just had our kitchen remodeled and they installed a calacatta white quartz countertop. After the installation, the appliance crew got epoxy on the quartz. The countertop installation crew came back out and used a resin powder to remove it. Is it safe to use a resin powder for cleaning or removing stains in the future? Sometimes in the sun, we can see a few dull areas in the countertop and I was curious is the resin powder would remove those dull spots.
Jeff (Sunday, 08 December 2024 20:34)
Mark,
Sent pics. We did see the slabs before fabrication and they were without these streaks. Thanks in advance.
Mark Ortiz (Sunday, 08 December 2024 16:32)
Belinda, sorry I missed your message.
Jeff. If only one slab had streaks, then it’s probably been there all along. I’d like to see it so email me at mark@ortizstonerepair.com and let’s see how I can help.
Jeff (Saturday, 07 December 2024 20:18)
Hi there, we have new Dolomite countertops and think they look great however the fabricator left dull white streaks (30+) in a perfect linear pattern every 3" on 1 slab. None of the other 8 large pieces have these streaks. Long story short, the company has gone out of business and we cannot get recommendations from them how to correct; we paid about 1/2 of the install thus far sand plan not to pay unless this is corrected if they come calling. We only noticed these streaks several days after install. The streaks appears dulled and are not removed with usual granite cleaners; we did get some Lustri Italiano etch remover and noticed (in a small area as a trial) that it seemed to lessen the streak. We are unsure what caused these unsightly lines and wish to correct. Any thoughts?
Belinda (Thursday, 17 October 2024 15:49)
Hi Mark, One hour ago the tile company crew finished installing a third countertop. First one was black granite that left white spots or streaks with anything acidic that contacted it. Not even giving a minute to clean up the spill or drip. That countertop was removed. Second was a dark grey quartz. This one had several rough spots that were determined to be a fault left during manufacturing. Third, the one just installed, is the same dark grey quartz. It was a new slab inspected by the tile company. It has very small white pits in about 15-20 places. Each about the size of a sharpened pencil lead or a little bigger. The installer said it is a manufacturing defect and can not be fixed. The installation company is coming next week and the owner says the spots could be filled in with epoxy. Please help. What are you thoughts. I am so frustrated. This was not a planned remodel but a year and a half long repair due to a water leak. The spots are small but very visible due to the dark color quartz.
Ida (Thursday, 12 September 2024 09:28)
Hi Mark, I’ve had a white quartz countertop for a couple of years. Two weeks ago I noticed a white ring that I didn’t see before. Any thoughts? Could this be a manufacturer defect or did someone put a hot pan on it or was it because of a corrosive substance came into contact with it? I’m driving myself crazy because I can’t figure out what happened?,
Thanks
Rob (Thursday, 27 June 2024 21:19)
My manufactured stone top in the kitchen has two small what looks like spill spots.. only really visible in the sunlight.. If you look at them from above nothing is visible but if you run your finger nail across the surface you can feel a very slight difference.. it being rougher.... Run just your finger across them and you cant feel anything.....looks like the shine has gone in these areas..... Any suggestions
Mark Ortiz (Thursday, 13 June 2024 06:17)
Kami… sorry I didn’t see your question. Try cleaning with acetone. If the red is a surface contaminant then it should come out. There are many products with red dyes that appear when exposed to moisture… just a thought.
Maryellen. White filmy spots huh? Because you said filmy, that means something on top. So try to scrape off with a straight edge razor blade. Next rub it with Denatured alcohol. Let us know if that resolved it.
Thank you both for asking!
Maryellen Kilkenny (Tuesday, 11 June 2024 20:20)
I have white quartz countertops for a year in a new construction home. I now noticed several small white filmy spots I can’t remove. I only use soap and water or the recommended cleaners by the manufacturer. I have contacted them but haven’t heard anything yet. I always wipe stains immediately. What could it be. Thank you.
Kami (Sunday, 02 June 2024 12:30)
Mysterious, tiny red dots have been appearing on our white bathroom countertop. When you wipe them off they leave a pink stain. Even magic erasers don't remove them. No one uses any red-colored products in the bathroom. Our contractor wondered if someone was using acetone nail polish remover, but no. This has been going on for weeks and we can't figure it out. Any insight?
Mark Ortiz (Sunday, 12 May 2024 13:34)
Hello Mel. My go to product is Granite Gold Daily Cleaner. There are other great cleaners, but I haven't tested them all, so I keep recommending Granite Gold. Go to my stone care tab and scroll down until you see recommended products. Good question.
Mel M (Saturday, 11 May 2024 09:00)
What do you recommend cleaning quartz with other than water and Dawn? Anything commercially available you like?
Mark Ortiz (Monday, 06 May 2024 07:19)
Hey there Paul. Truly sorry about that. My first thought was...change the body wash! Or at least keep it out of your eyes. Haha...not funny? Ok, so there is a chemical in the wash that effects the man made material. If its acidic, then you might have the man made material with marble instead of quartz. Test this by leaving a cut lemon on the surface for about 10 minutes. If the stone dulls, then you probably have this type of product. Inform your supplier and they should either get you a quartz counter instead. Many suppliers are not aware of this. You can also get it professionally refinished and polished. May cost about $750-$1200 depending on company. If it did dull from lemons then you will need to treat it like polished marble. If you are messy, then replace it. If you are carful, then re-polishing works great.
paul (Saturday, 04 May 2024 04:48)
Help! We recently had new vanities installed in our bathrooms. The countertops are man made stone. Both countertops were flawless when installed. Recently, I was trying to transfer body wash from one container to another. During the process, the soap spilled on the stone. I cleaned the product off of the stone, but now there are dull spots where the soap contacted the stone surface. Can the dull spots be repaired or is there a new countertop in my future?
Mark Ortiz (Sunday, 28 April 2024 06:58)
Dawn. Sorry for the late reply. I sometimes miss the requests and then notice way too late. Your spots, swirls and blotches are common. The marks from the rubber pads usually occur if the stone is slightly honed or not 'highly' polished. I think your solution is to "lightly" clean it with barkeepers friend (powder type) and water, lightly cleaning in circles. This will remove most of the issues. The natural light reflection will always show blemishes, so don't think it needs to look PERFECT. In my opinion, Quartz is not perfect. Hope that helps you.
Mark Ortiz (Saturday, 27 April 2024 09:29)
HI Terry. I completely understand and know exactly what you are talking about. Many of my work shirts have those same holes. It would be perfect for those 1980's flash dance outfits the girls used to wear. Haha. But not for our new shirts that are crazy expensive! I had a customer that actually thought they had moths and tented the whole house! The solution is to refinish the top edge with either sand paper or granite diamonds with a variable speed grinder polisher. If you are super mechanical and are familiar with this technique, then Harbor freight tools will have a one time set up for you. I'll give you more details if you decide to do it yourself. Or you can have a professional do it. The cost will be around $500-$700. Let me know how I can help you further. Mark
Terry (Thursday, 25 April 2024 19:34)
I love the design and look of my granite countertops . The only problem I have with them is that they are ruining the front of my shirts day after day. They are putting tiny holes where my shirt hits the counter side. I ran my finger along the side and it is a tiny bit rough. What can I do to smooth this out? I don’t wanna ruin the look of the counter..
Dawn V Leeman (Wednesday, 10 April 2024 18:20)
I just had Emerstone Supreme quartz installed in my kitchen about a week ago. I have noticed all the blotches when the natural light hits the surface. I have small rings and swirl marks as well. Today I put a meat slicer on the counter with rubber 'feet'. When I removed the slicer it left black 'feet' marks on the counter. I tried to clean it with Weiman quartz cleaner but it didn't come out. I also tried windex but no results. I am extremely scared to use the counter at all because everything marks it. I thought quartz was the best selection for a busy kitchen as it is supposed to be non porous but so far this is not true. Help! I live in NJ.
Karen Jacob (Wednesday, 10 April 2024 07:11)
Hi,
My countertop is black quartz brand new and has wipe marks and cloudy areas. It looks great when you stand directly over it and look down but with any lighting Its hazy and streaky. What product will remove the wipe marks and even out the blotchy areas?
Mark Ortiz (Friday, 15 March 2024 17:18)
Hi Teri. Based on your description, I can’t determine what exactly is going on. Email me mark@perfectgranitesolutions.com
A few pics and I’ll give you my best advice. Thanks!
Terri (Thursday, 14 March 2024 19:23)
Hi. I just had quartz installed in a kitchen renovation last week. The counters looked fine for a few days, but today, I noticed a straight gray line right over the wood separating the two cabinets below it. It looks like adhesive seeped into the quartz. We just had the tile backsplash installed today, so I’m pretty concerned that I didn’t see this sooner. It may have been there for a few days, but the counters were covered up due to all the other work going on, so I didn’t see it. It definitely wasn’t there for the first few days. Any advice would be very much appreciated. Of course, I will show our contractor and he will contact the quartz guys to see what they say, but I’d like an independent expert to weigh in, in case they try to tell me nonsense. Thank you very much.
Melissa Strickland (Monday, 11 March 2024 11:02)
Hello,
We had some small chips repaired by the company that installed our counters and the area now looks cloudy. What could this be? Also, in general lots of inconsistent reflection as we have a lot of natural light. I’m guessing this is normal. I also noticed today when I moved a decorative tray off my island that I can see the outline of it. It seems you can’t put anything on quartz counters. We got Pental so it’s not a cheap brand and I’m extremely careful and picky. We don’t even put glasses on the counter without a coaster!
Denee L (Monday, 12 February 2024 15:59)
Hi I just moved too my new apartment in January and I have Quartz countertops. This morning I’m cleaning the counter and there are these fine crystals along the edge of the countertop. I’ve never felt them before and I wipe the counter tops daily. I’m not using any harsh chemicals just a dishcloth and warm soapy water. As I’m wiping I thought it was sugar but kept feeling it and I noticed it’s all along one edge. Should I be worried?
Mark Ortiz (Wednesday, 13 December 2023 09:49)
Melissa,
Email me pics at mark@perfectgranitesolutions.com
I’ll review and give you some directions.
Melissa (Wednesday, 13 December 2023 05:19)
Hi Mark! I’d love some advice about our quartz countertop. When it’s not in direct sunlight, it looks perfect, but once the sun shines on it, I can see circular marks in different places on the island slab as well as seemingly streaky water marks? The circles are unusual because they have a pattern inside of them-additional symmetrical lines extending out from the middle and more circles. There are also several half circles-one around the faucet, and one on the outer edge. We only clean it with very dilute soapy water with microfiber towels. I have once tried to clean a small bit with a touch of baking soda and water and a non scratch sponge. You can’t feel the water streaks or the circles. We live in upstate NY, do you have any recs for us?
Angie (Monday, 27 November 2023 09:20)
Hello!
We just moved into our new build and the builders have installed quartz countertops in the kitchen and bathrooms, called Bianco Tiza. From the get go I’ve noticed that the countertops feel rough and almost like there is just a layer of dust or sand on it- even right after cleaning. There are also some spots that just feel more rough and bumpy than others- I can visibly tell there are some raised spots but I’m not sure if it’s from paint the workers accidentally put on there if they painted the walls again after installing.
I’m not sure if it needs to be sealed or if there’s a product I can use to get it to feeling smooth! Super frustrating, I have reached out to the builder as well to see if there’s anything they can do but as I am waiting to hear back thought I would try here!
Hi (Tuesday, 07 November 2023 08:51)
Thanks! Can Tuffskin be installed yourself or do you need an installer?
Mark Ortiz (Sunday, 05 November 2023 08:27)
HI,
Yes! Tuffskin will make it smooth and beautiful again. If you are in California or Colorado, email me at mark@ortizstonerepair.com If you are in another state, contact Tuffskin, Nevada and they will connect you with an installer.
Thank you for participating in the comments... Mark
Hi (Sunday, 05 November 2023 08:20)
Thanks for your help! The whole surface is completely gritty (there is no smoothness to it at all) now. Will the Tuffskin Surface protection make it smooth again? I basically just want something to make cleaning easier/protect the surface from spills/further damage. Right now you can’t even wipenup water because there is no outer barrier on it left.
Mark Ortiz (Friday, 03 November 2023 06:51)
Hi “Hi”. I like your name. Is your last name Bye? Couldn’t guess your middle name �
I’m guessing you have a Quartz with calcite stone that is dulling from the acidic cleaners, or there is a cleaning product leaving a residue on it.
First clean with Barkeepers Friend powder and a green scrub sponge. Do it lightly , rinse and dry. If it looks better then do the whole surface. Do not scrub hard, it might permanently dull it.
The only product I recommend is Tuffskin Surface protection. Go to my main page and click Colorado. Click Tuffskin. Email me if you have more questions.
It can also be repolished by a professional only. Email me pics and your location, and I’ll try to help.
Mark Ortiz (Friday, 03 November 2023 06:44)
Barbara, It is common to see colored spots which are most likely contaminants of other colors in the processing plant. If the repair specialist can drill out and refill so it blends in with the surrounding stone, then it truly is not a big deal. Quartz finishes usually allow spot fills to blend well. Allow the repair to be made and then evaluate again. Don’t replace it yet… allow them to make it look right.
Hi (Wednesday, 01 November 2023 12:28)
Hi, my countertops are extremely gritty due to prolonged cleaning with cleaning vinegar (months of excessive use). I know that the acid can wear away the luster and top of the quartz, leaving them with a terrible feeling/look. I can't even clean them anymore! Is there a way to fix this without completely replacing the countertops? Is there a DIY epoxy resin I can use to get a smooth finish again?
Barbara (Thursday, 26 October 2023 11:01)
Hello! We had quartz countertops installed in our kitchen and a half bath last week and there are visible small pink dots throughout (8-10 at random). They look like a dot from a fine point pink sharpie. The installer claims they are part of the natural process and that they could resolve it with a method of drilling a small hole and filling it in, etc. and are treating the issue like it's not a big deal and these spots are inherent properties. The showroom sample and the samples we checked out did not have this type of issue. We didn't pay $9K for new countertops that have bright pink spots and need fixing or altering. Is this a common issue??
Mark Ortiz (Tuesday, 22 August 2023 14:50)
Vonita, sorry I didn’t respond quicker. Dorian, you and Vonita may have the same issue. It is difficult to give a solid answer but I’m thinking both of you need to have it professionally inspected and polished. Not sure what state you live in, but let me know and I’ll try to help here in Southern California or Colorado. If in another state I may have a referral.
Dorien (Monday, 21 August 2023 14:13)
I had my quartz countertop installed last week. In natural light I can see what looks like a waterspot under the resin. What is this and what can I do about it?
Vonita (Monday, 24 July 2023 16:53)
My quartz kitchen counters have dull circles and some dull streaks. Can this be repaired?
Mark Ortiz (Saturday, 01 July 2023 15:30)
Hello Steven. The solution is to have the “plugs” of the same material cut out from the remnants. The fabricator uses a core bit slightly larger than the actual hole. Then the plug is grounded until it fits nicely. A colored epoxy then glued the plug into place. (I use a 2 part epoxy because it gives me about 60 more seconds before it sets). It must be very flat. Do not attempt to sand the plugs flat unless the specialist is an expert on Quartz polishing. That should do it.
If no plugs are available to match, then an expert in epoxy color mixing can patch it.
Hope that helps!
Steven mihovich (Friday, 30 June 2023 11:23)
our new house has Montreal countertops put in. the bathroom countertops were cut for three holes but we have a single lever Fawcett ordered. have do they fix the holes in the quartz
MarkOrtiz (Sunday, 18 June 2023 19:03)
Hi Cari - I can't visualize a 'bump' that you are talking about. Send me a picture to info@perfectgranitesolutions.com and I'd be happy to help you. Mark Ortiz
Cari (Friday, 16 June 2023 15:00)
Hi, the side of my island has a bump. and i can see a line. i was told this was due to the machining process. this is the second time it's been replaced (first time was due to another defect). I didn't notice a bump or line on the side of the last one, so i am skeptical when they tell me all islands have this.